Company Insight
Sponsored by Nissei ASB
Bag-In-Box for Water Servers
Polyethylene Terephthalate (PET) made its first impact on the container molding industry via carbonated soft drinks during the late 1970’s just as Japan’s Nissei ASB Machine Co., Ltd. was founded. In those early days only three machine manufacturers existed globally that produced equipment capable of stretch-blow molding this new material.
At CANPACK, we are convinced that exceptional products deserve exceptional packaging. In the spirit of the saying "differentiate or die", manufacturers and brands cannot afford mediocre product packaging. This is why, in order to create and maintain long-term consumer awareness, it is crucial to look for packaging ideas that will allow products to shine on the crowded store shelves.
Nissei ASB Machine Co., Ltd., founded in Japan in 1978, quickly became the world’s leader in 1-step injection stretch blow molding equipment by providing the industry with diverse technologies for production of high quality, unique and specialized containers, in PET and other plastics that help protect our health and environment.
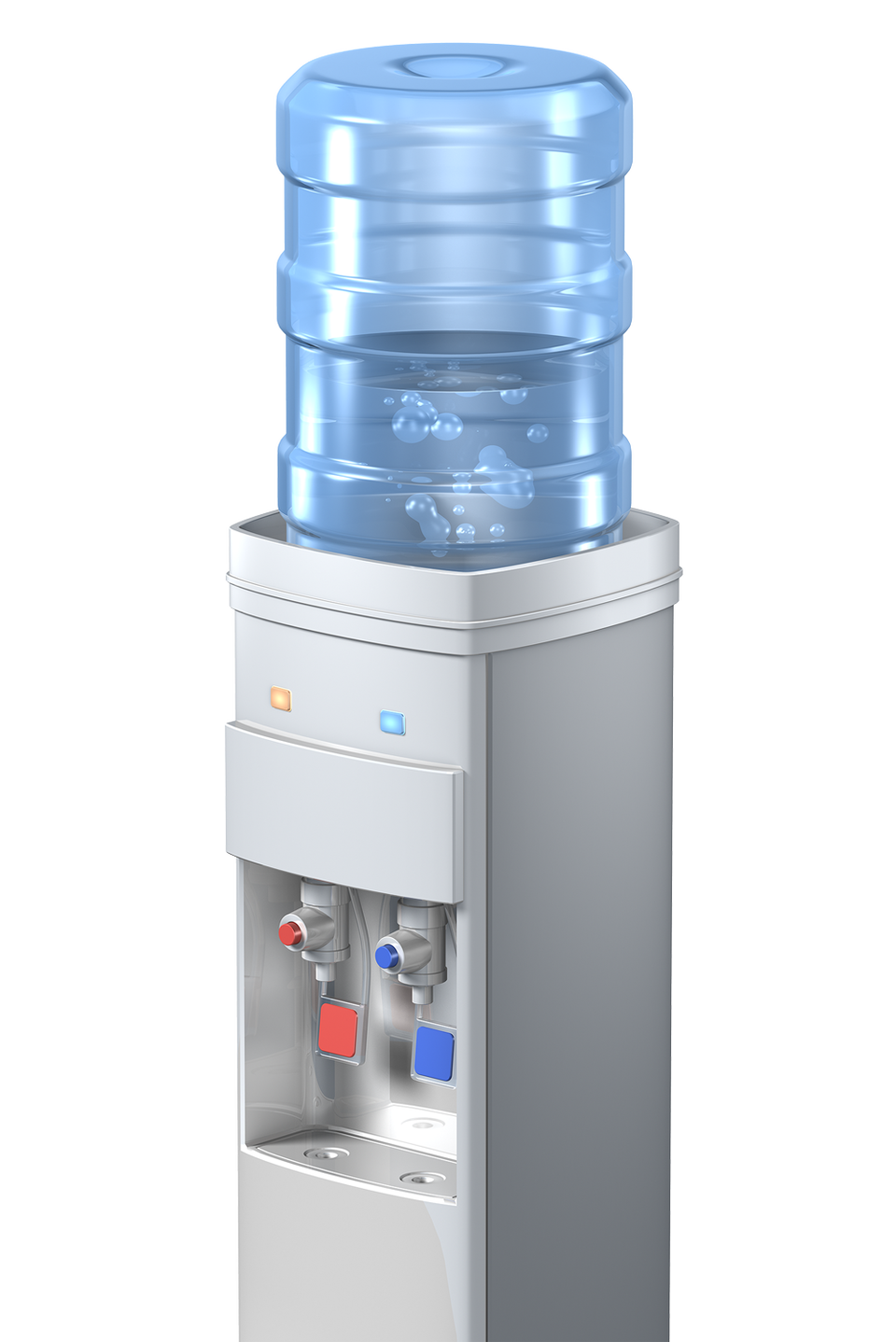
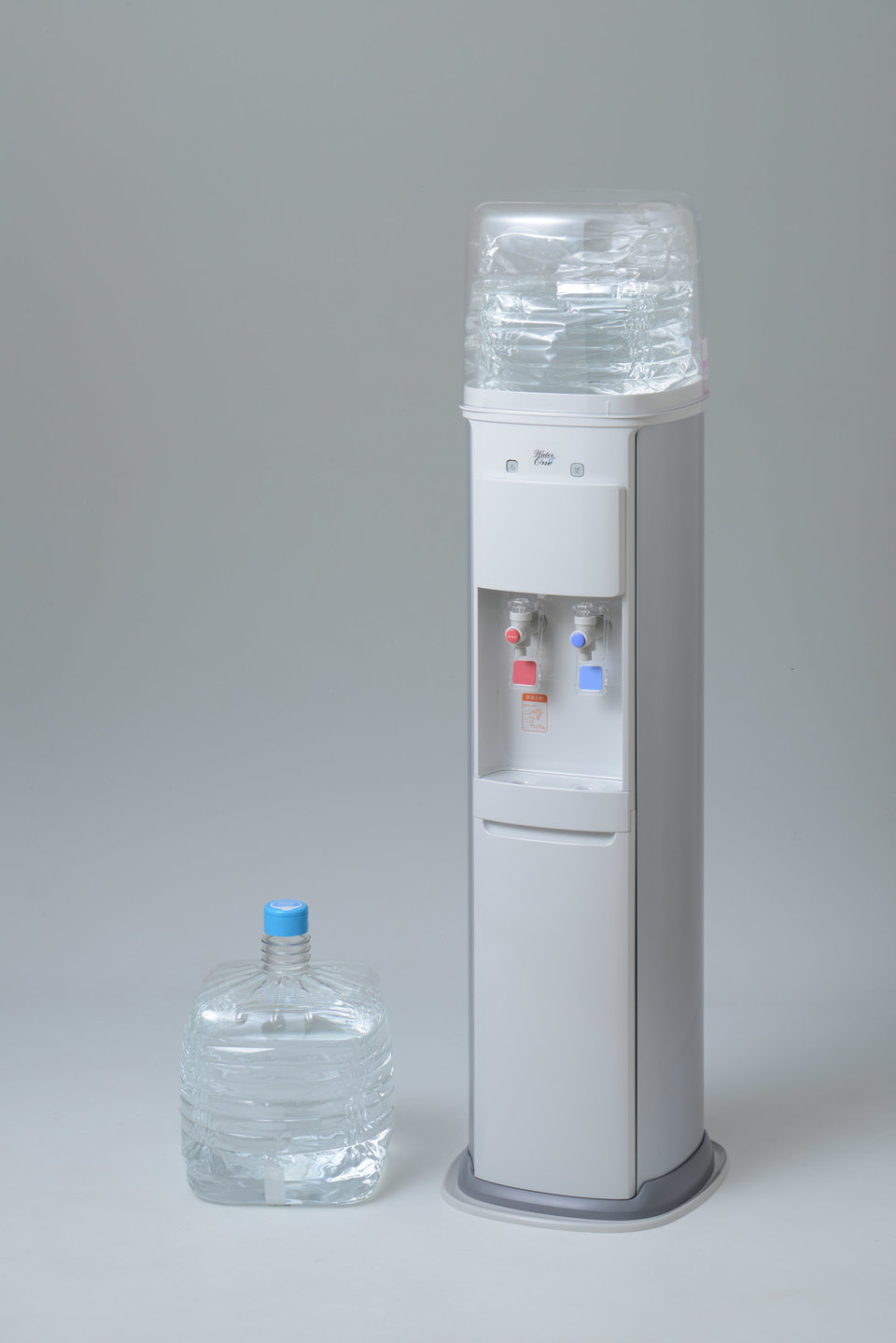
Figure 1- Conventional water server
Figure 2- Water Server & Bag-In-Box container
We are all familiar with the office water cooler and the 12-20-liter (3-5 US gallon) bottles that sit atop them. Most are molded in polycarbonate (PC), others may be PET – all are typically thick and heavy (up to 800 grams) as they are designed for multiple return and refill.
Fully returnable and refillable packaging is a laudable goal, though reality often falls short of the target in terms of both environmental and economic targets, and for health, the purity of basic essentials such as drinking water must take priority.
Returnable and refillable containers suffer scratching, breakages and repurposing that greatly shortens their effective life so stocks must be continually replenished. Meanwhile, returning large empty containers to the filling plant generates economic and environmental penalties via additional transportation and the chemicals, water and energy required to safely sterilize them.
Some regions have introduced one-way 15-20-liter bottles molded in PET – generally of a similar design with the standard container with weight reduced to about half that of its returnable equivalent.
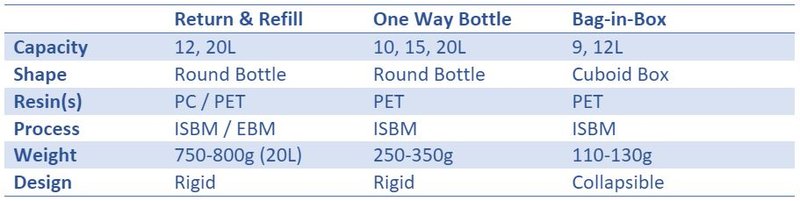
Table 1- Container types for water servers
Environmentally, one-way conventional bottles are the least desirable option. Their round design and stacking difficulty mean wasted volume in transportation while repurposing of used bottles may not be an option as they lack durability.
Nissei ASB has been a key player in developing the Bag-In-Box 12-liter water container that has gained huge popularity in the Japanese market, providing a wide range of benefits at the point of delivery and consumer safety;
- Generally supplied via online shopping services including Rakuten and Amazon.
- Easily stacked cube shaped outer carton.
- No special delivery or collection trucks required.
- Fully recyclable outer cardboard carton.
- Lightweight PET inner container reduces material usage, easily crushed for collection through municipal recycling programs.
- Full protection of water from airborne contamination when used with compatible water dispenser system.
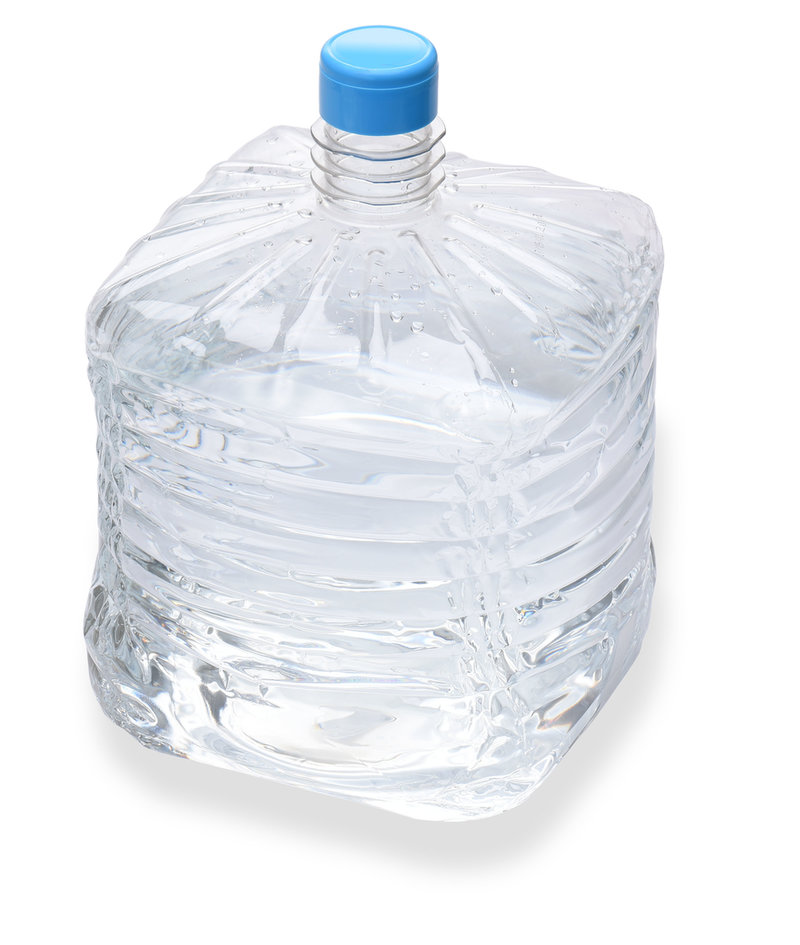
Figure 3- 12-liter Bag-In-Box bottle out of its box
This last point has generated huge recent interest as consumers have suddenly become very aware of improved hygiene to mitigate the spread of airborne diseases.
As water is dispensed from a conventional solid bottle, the familiar glugging of air bubbles into the bottle indicates it is being replaced with air drawn from its surroundings that may be carrying airborne dust, bacteria or viruses.
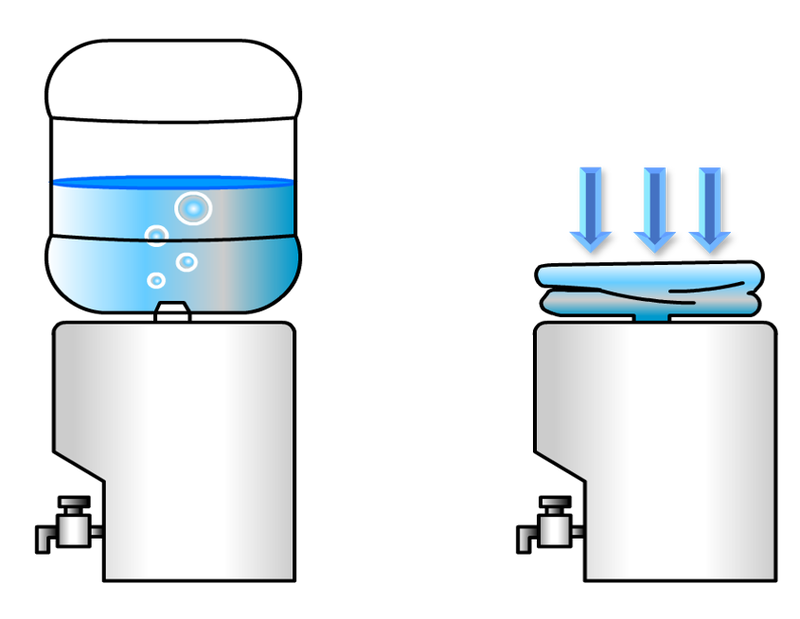
Figure 4- Ambient air cannot enter the collapsed bottle
The Bag-In-Box is distributed to homes and offices within a cardboard outer carton, then unpacked by the consumer and lifted into the dispenser in the normal way.
With the Bag-In-Box container installed into a compatible dispenser, backflow of air is prevented. Due to the thin wall and rib design of the container, as water is dispensed the bottle simply collapses with no headspace developing. Result - no potential contamination is drawn back into the container.
To answer growing demand for this product, Nissei ASB recently expanded the capabilities of its PF36 Series molding machines to include the all-new PF36/9-12000 model. With this addition to the line-up, productivity improvements mean that for the same output by the previous method, floor space has now reduced by 70% while investment cost has reduced by 35%.
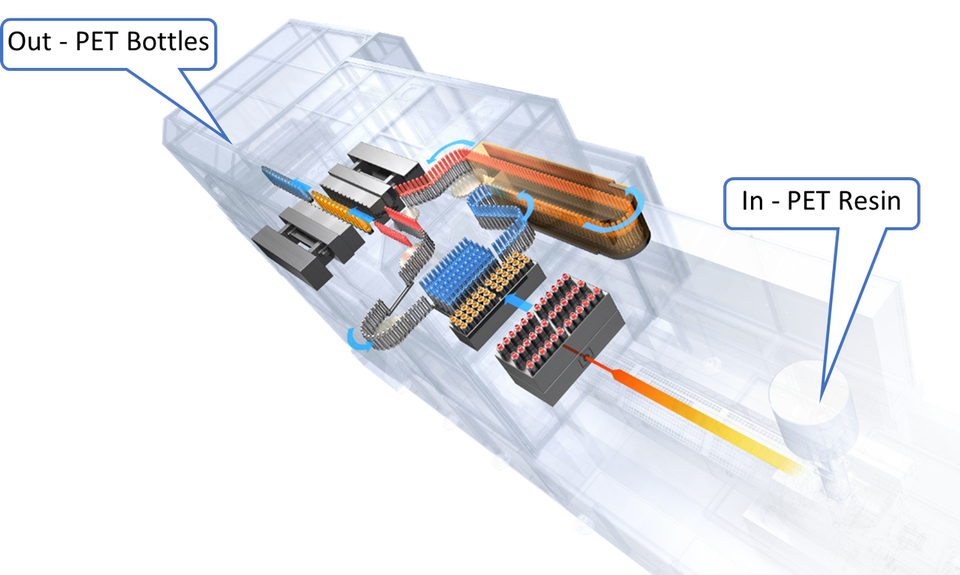
Figure 5- Material flow through the PF36 series machine
The PF36 molds containers by ASB’s uniquely efficient 1.5-step injection stretch blow molding process producing its own customized preform, so no external purchase is required. In fact, full bottle cost by the PF36 is less than the purchase price of just the preform used by 2-step systems.
The 1.5-step molding system is an original development of ASB that has captured the market for versatile, compact, high quality PET bottle molding. Because all molding is conducted in one machine, the interior of the container is guaranteed to be clean and sterile, while container quality is significantly higher than can be achieved by the 2-step molding process.
ASB is the world leader in 1-step injection stretch blow molding, its turnover accounts for 15% of world-wide sales in all PET container production. A network of 16 sales and service subsidiaries and a further list of over 40 sales agents completes global coverage and ensures that ASB customers in over 130 countries are never far from sales or technical support.
Background image blablablablablablablabla