Bottling and packaging of drinks and foodstuffs are the final steps in the value-added chain of food production. Avoiding downtime is a major challenge, because downtime means losses. Since even the shortest amount of downtime, so-called micro-stops, can reduce a system‘s effectiveness significantly. Improvements are only possible when the key causes of downtime can be identified.
Within this context, a Line Management System provides a great solution and helps to determine the causes of downtime. Plant Acquis iT LMS from ProLeiT offers an add-on for the production data management system Plant Acquis iT, thus enabling simple access into the world of Line Management.
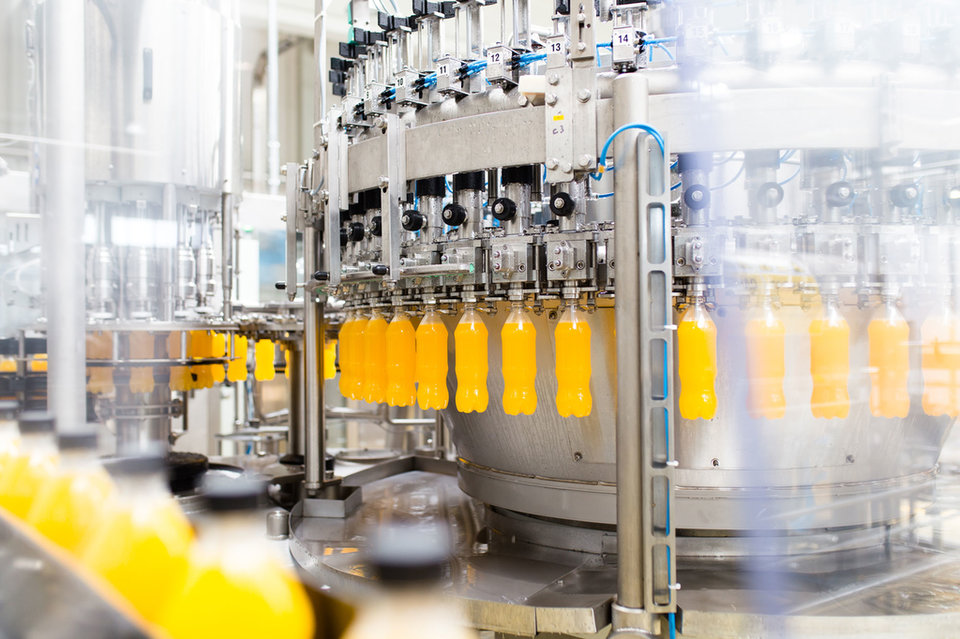
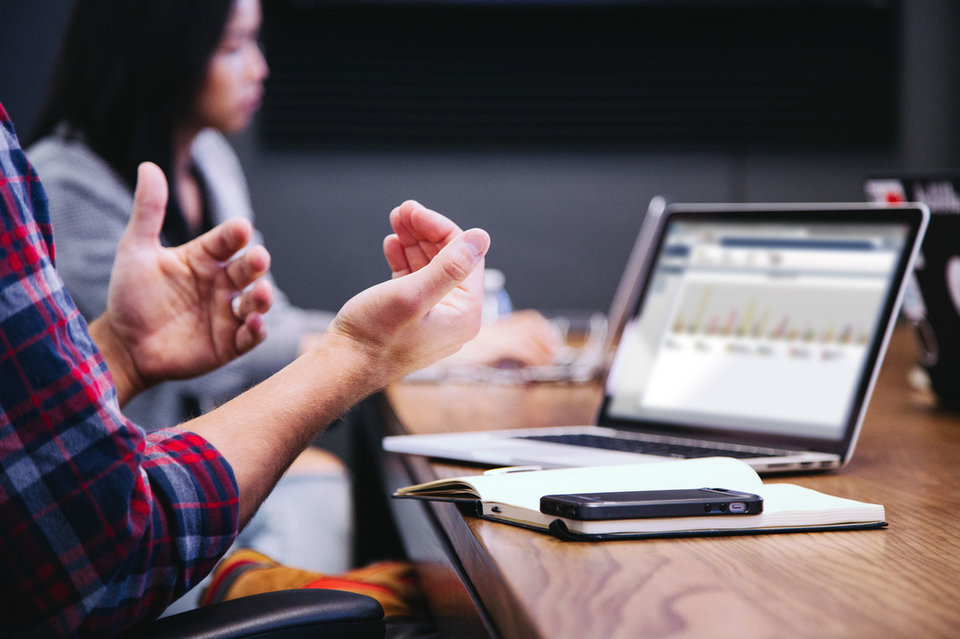
Minimizing downtime, maximizing plant efficiency
Plant Acquis iT LMS records system and machine downtime automatically, reliably and exactly. The causes of downtime and other system or order-related data can be entered at any time manually via drop-down boxes. And predefined causes of faults can be enhanced and extended according to your individual needs. The threshold value for microfaults can also be defined individually.
Line shutdowns
Line shutdowns
LMS Dashboard Fillingliness
LMS Dashboard Fillingliness
The entire data can be analyzed down to the finest detail with the help of the drill-down-function: downtime periods can then be arranged hierarchically with varying levels of detail from the overall bottling plant to individual units. Plant Acquis iT LMS then outputs the generated reports at every office PC in the Intranet or on smartphones and tablets. Furthermore, customer-specific data can be entered and evaluated.
Optimum performance thanks to comprehensive functions
The extensive range of the add-on Plant Acquis iT LMS addresses the needs of varying professional groups in the process engineering industry: for instance, production managers profit from the fast, web-based lists stating the causes and times of faults, while supervisors can use a generated report to gain an overview of the current plant situation before starting a shift. The userfriendly, menu-guided user interface allows plant operators to quickly and, in particular, consistently determine the causes of faults. Paper-based recording, which was always prone to errors, is now a thing of the past. Maintenance staff can extend Plant Acquis iT LMS simply by configuring parameters. They are also provided with a quick overview of a plant‘s weak points and can identify its potentials for optimization.
LMS Shift Protocol
LMS Shift Protocol
Electronic shift and
order protocol
Electronic shift and
order protocol
Contact Information
ProLeiT AG
Einsteinstraße 8
91074 Herzogenaurach
Germany
Website: www.proleit.com
Email: info@proleit.com