design
Design
A weight-loss programme for plastic packaging
Companies are under increasing pressure to reduce the amount of plastics used, leading to many working towards ‘lightweighting’ their packaging designs. Selig's Sales Director, Peter Tindale, highlights the results that can be achieved when this design approach is coupled with induction heat sealing.
All Images: Dassault Systèmes
Plastic packaging
plays a vital role in our daily lives. It facilitates the transport of food and beverages and protects them from spoilage. Furthermore, well-designed packaging can help to keep the prices of these products down, since it can reduce the cost of transport, distribution, storage and retail.
Despite these benefits, however, few sectors have come under greater scrutiny from governments, the media and consumers in recent years than those that manufacture, or make extensive use of, plastic packaging.
This scrutiny can be attributed to an increase in the awareness of the impact of plastics pollution on the planet. Recently, for instance, the Ellen Macarthur Foundation estimated that, on the current track, the weight of plastics in the world’s oceans could exceed that of fish by 2050. The issue is compounded by the fact that, at present, only some 10% of plastic packaging is ever recycled.
Lightweighting increasing in importance
As such, many companies are looking for ways to reduce their reliance on plastics for the packaging of their products. An approach known as lightweighting – whereby the amount of plastic used to create a piece of packaging is reduced incrementally – has become an increasingly important tool with which to achieve this aim.
Nestlé, for instance, has cut the weight of its water bottles by 22% over the last ten years and, through clever design, avoided the use of more than 142,000 metric tons of packaging material by the end of 2019, compared with 2015.
Lightweighting yields numerous other benefits. As less packaging is used, raw material and production costs are reduced. Lighter products are cheaper to transport. Furthermore, lighter packaging enables couriers to carry more products on each delivery round, which is of increasing importance as e-commerce continues to grow.
The perfect combination
Packaging must be robust, tamper-proof and leak-free if it is going to provide customer satisfaction. To achieve this, whilst still lightweighting the packaging and closures, producers have turned to a variety of methods. These include production line changes, such as compression molding technology and packaging redesign to remove unnecessary features.
Combining lightweighting with induction heat sealing has stood the test of time, as it creates a strong, hermetic seal that has many benefits.
Induction heat sealing uses a laminated liner, which is placed inside the container closure. The essential components in the seal include an aluminium layer and a heat seal layer - specific materials being chosen on a case-by-case basis, depending on the material of the container and what is inside the package.
Pressure is needed to ensure the liner has an even seal to the container rim, and this is generated by the torque heads of the capper when they place the closure onto the filled container. Heat is applied and the heated seal adheres firmly to the rim of the container as it cools.
Timing is crucial if an effective seal is to be formed. Likewise, too much pressure – or cap-on torque – between the liner and bottle neck, excessive heat to activate the liner seal surface or extended dwell time under the induction coil will leave users with a seal that cannot be removed with ease. On the other hand, not enough heat, pressure or time will result in leaks or the ingress of contaminants.
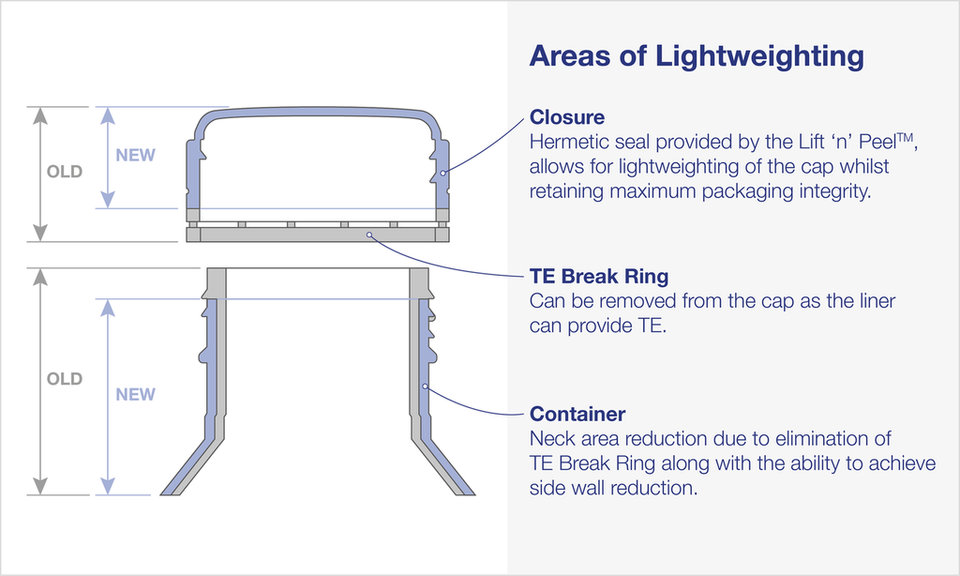
CPG packaging manufacturers can create a 3D model of the packaging design in a real-world setting, and review and enhance it quickly and easily.
If all of these variables are managed correctly, then the results that can be achieved are impressive. As well as being fast, induction heat sealing is relatively inexpensive and when the seal is removed from the container, it leaves the packaging clean and ready to enter the plastics recycling stream.
Furthermore, these seals are light, and enable mass to be shaved from other areas of packaging. Owing to the robust hermetic seal generated by the process, caps can be lightweighted. Break rings are no longer necessary as tamper evidence is provided by the seal.
Finally, because there is no longer any need for the break ring, and because the cap is now lighter in weight, the size of the container's neck can be reduced, and it can be formed from thinner gauges of material.
As well as being fast, induction heat sealing is relatively inexpensive
Significant plastic packaging reductions achieved
Induction heat sealing enables the use of polyethylene terephthalate (PET) bottles with thinner walls for the packaging of tomato ketchup, for example. In addition, caps for these bottles can also be lighter and tamper bands are no longer needed.
The combined impact of induction heat sealing and lightweighting can be seen in the dairy sector. In 1992, a one-litre high-density polyethylene (HDPE) bottle weighed a fraction over 34g and featured a 38-mm polyethylene (PE) cap weighing 3.1g. By 2013, thanks to the combination of induction heat sealing and lightweighting, a HDPE container of the same size weighed just 26g, its cap just 1.5g.
As well as working to reduce the weight of their packaging, companies also want packaging that can be re-used at the end of its working life. To this end, cap liners that are completely recyclable are being used widely in a range of industries.
Companies, including Selig, are also looking at the possibility of manufacturing liners from polypropylene (PP) and PE, to match the caps of containers, so they can be recycled more easily.
Significant environmental, cost and functional benefits can be achieved using the formidable combination of lightweighting approaches and induction heat sealing. As pressure on suppliers and retailers to reduce the amount of plastic packaging they use continues to grow, so too will the significance of these complementary technologies.
Cover image: Dassault Systèmes