
UV Curable Ink Jet Inks
Energy curing technology (also called radiation cure or UV/EB cure) has been a significant presence in the graphic arts industry for over 30 years. This is true in a wide array of market segments, including heavy penetration into the flexo, litho, letterpress, screen, and letterset ink areas. This is also valid for extending usage in the area of UV curable inkjet inks.
While still smaller in terms of total volume compared to the more traditional litho, screen, and flexo markets, this is a growing application. UV curable ink has already become a very important part of the wide format arena, with forecasts predicting continuous growth. The instant cure, pigmented weathering stability, adhesion, better chemical resistance, low VOC, and overall print quality are major drivers. The lack of drying (except under exposure to high intensity UV light) also is a major driver due to far reduced inkjet head clogging and the lack of purging needed to clean this out for water and solvent based inkjet.
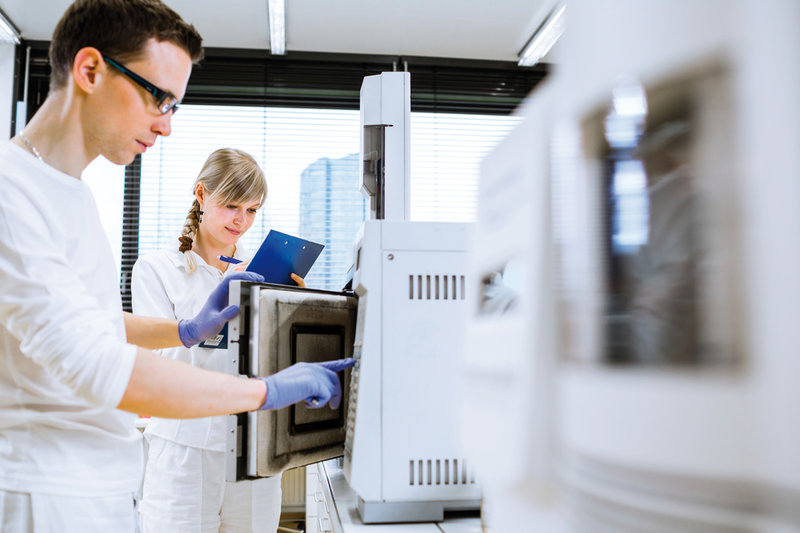
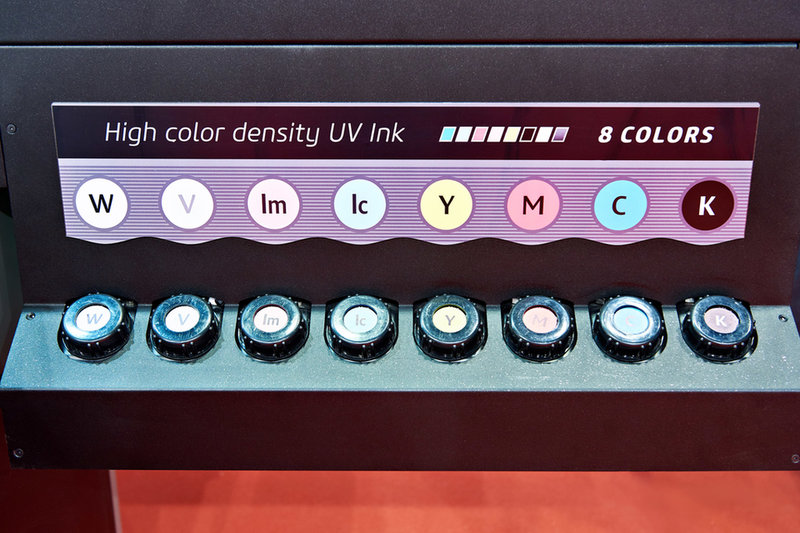
Formulation Issues
Inkjet inks are considered quite difficult to formulate, given that some of the performance requirements are mutually exclusive to each other.
The biggest formulating issue with inkjet inks is low viscosity. Typically the usual required range is 10-20 cPs, but this is at the elevated temperatures that ink-jet runs, typically around 40-45 degrees Celsius. Unfortunately, most low viscosity acrylate functional materials are reactive diluents. These are low viscosity, but have low functionality.
Low surface tension is needed to promote flow and wetting in the inks. Low surface tension also promotes adhesion to plastic substrates, which tend to have low surface tension surfaces.
Another important aspect for UV curable inkjet is pigment wetting, since the major growth is for exterior durability applications. Therefore, the difficult aspect here is to get reasonable pigment wetting combined with low viscosity. Typically, the pigment wetting acrylate functional materials used in flexo or offset are too high in viscosity. Pigment wetting in inkjet is achieved through use of hyperdispersants. However, some stability problems can be seen under common pigment dispersion techniques (as well as the high temperature and high pressure of the inkjet heads), so use of additional stabilizers might be needed, for example GENORAD* 16 or similar.
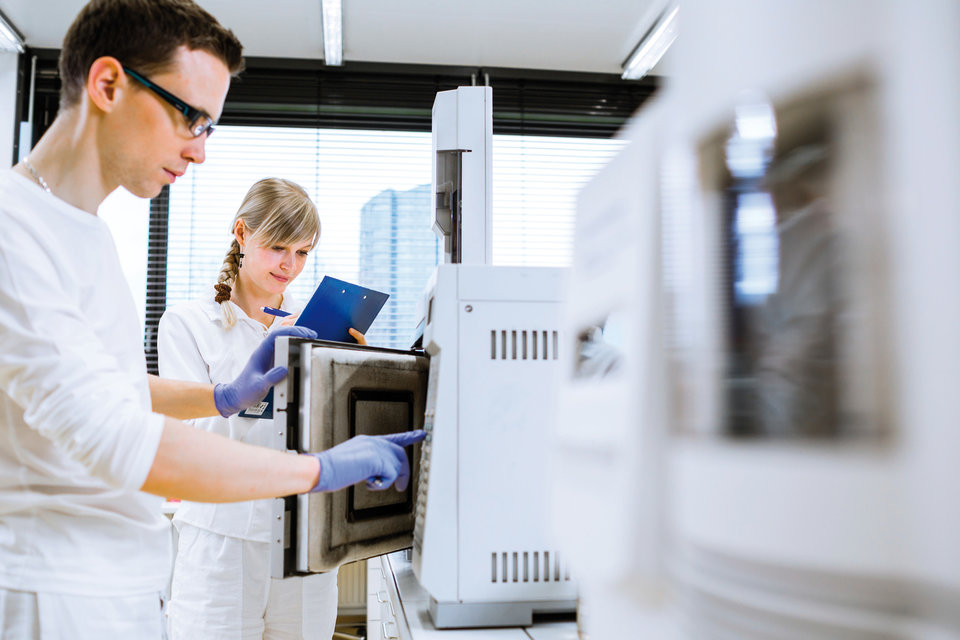
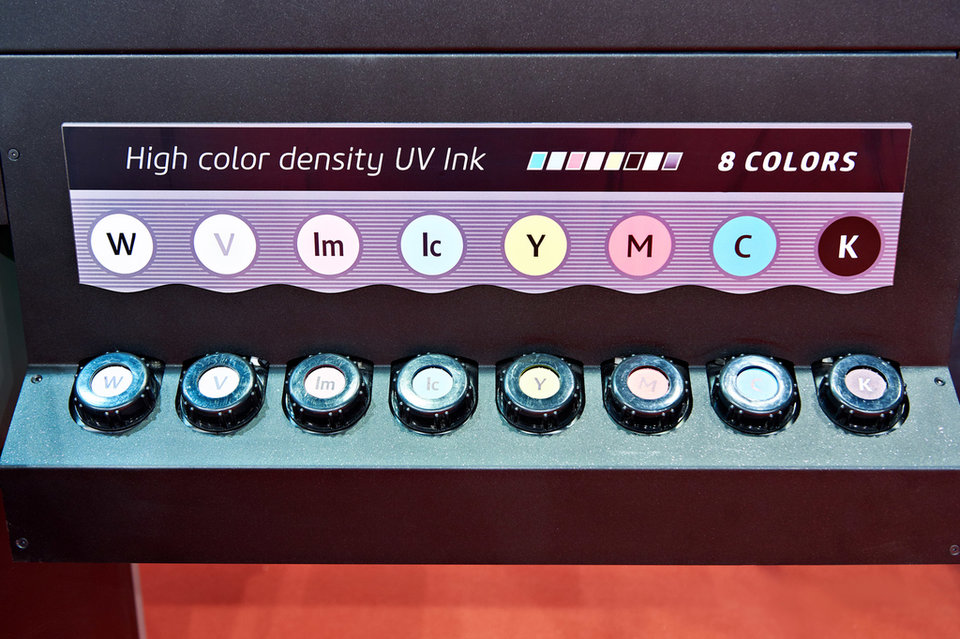
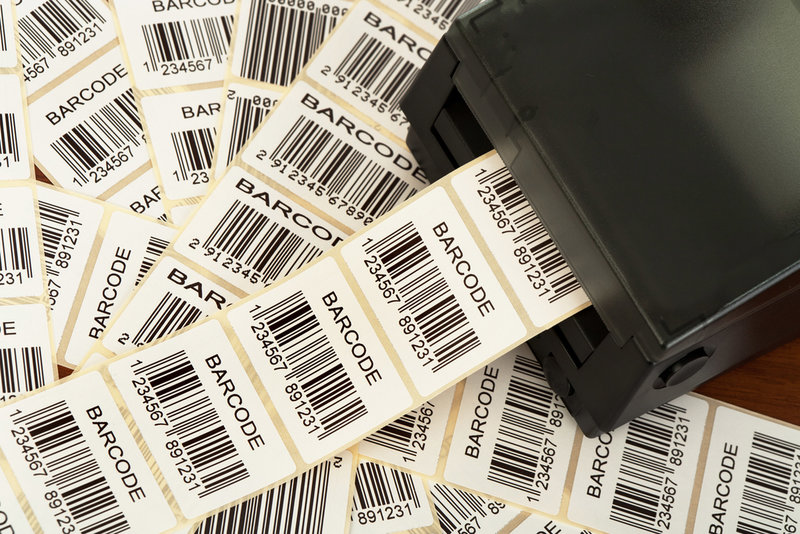
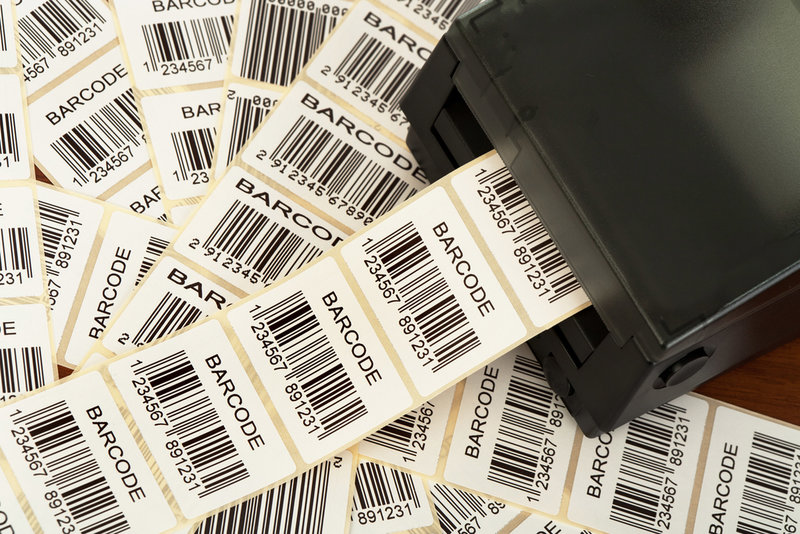
Wide and grand format applications are often used for banners and signs so exterior weatherability is often needed. The durability requirements are rarely for multiple years, but months are needed. Aliphatic backbones are still usually required.
Cure rate is less of an issue with wide format compared to industrial marking inks and typically runs less than 50 fpm (and often quite a bit slower than that). However, the low viscosity requirements mean that high concentrations of low viscosity, low functionality materials are utilized, which adversely impacts cure rate. Faster curing low viscosity oligomers like amine modified polyether acrylates (GENOMER* 3364 and GENOMER* 3497 for example) are often used. In addition, amine synergists are also needed for faster surface cure, and examples here would be GENOMER* 5141, GENOMER* 5161 or GENOMER* 5275.
Flexibility can be an issue since most of the wide format banners are printed on plastic film substrates. Use of monofunctional products can help here.
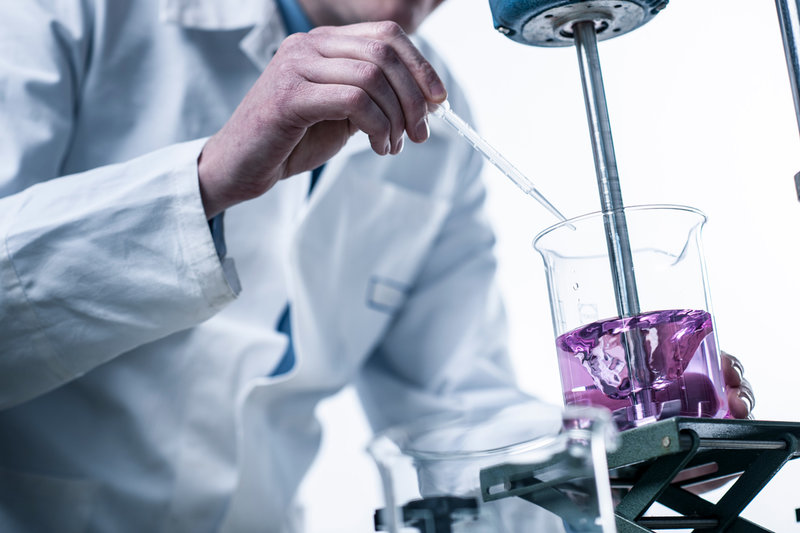
In conclusion, UV curable inkjet applications are a rapidly growing arena in the energy curing market. Formulating these inks is still a difficult challenge and the use of specialty acrylate functional reactive diluents like isodecyl acrylate; 1,6-hexanediol diacrylate; monofunctional aliphatic urethane acrylates; ethoxylated trimethylolpropane triacrylate; and alkoxylated pentaerythritol tetraacrylates can help with the difficult adhesion, flow and printability performance attributes needed. Contact RAHN for additional and more detailed formulating information on UV curable inkjet inks and download our Lab Report from our website.
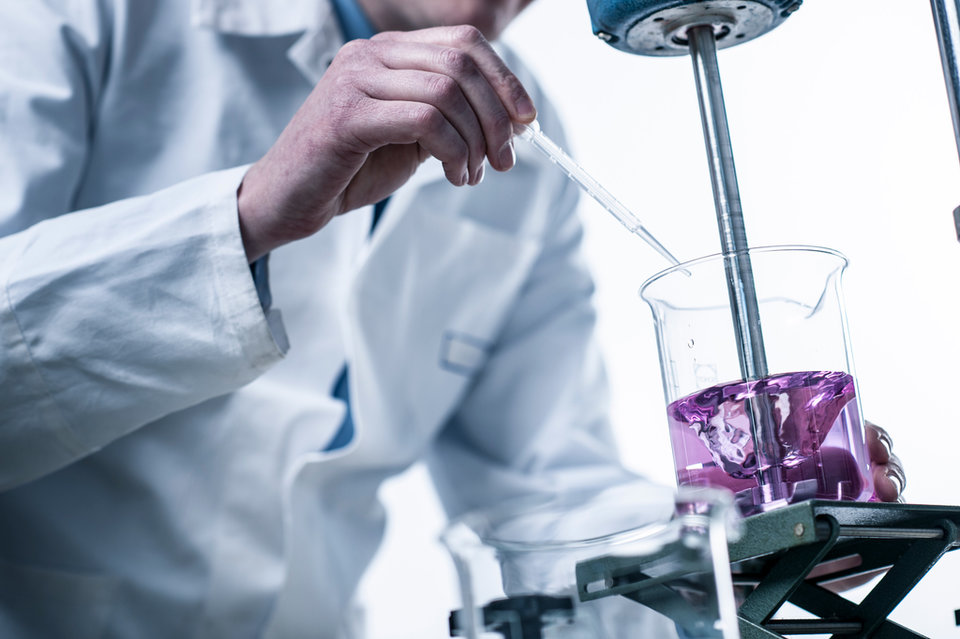
Be inspired
Our customers create amazing results with our raw materials for digital inkjet printing – no matter whether gloss, matte, or even 3D effects. What’s more, they can be used to print on almost any material. Whether, paper, glass, wood, plastic or metal, we have the right products to meet all sorts of needs and technical requirements.
Eye-catching food packaging
Food packaging jostles for customers’ attention on supermarket shelves and in the aisles. Our specially developed products with their high molecular weight ensure that the inks contain no undesirable substances that might penetrate the packaging. This keeps the food safe and lets the advantages of radiation-curing ink systems shine out for all to see.
Shape-retaining workpieces created with 3D printing
Our customers not only use our products to create 3D effects, but also generate robust workpieces with their 3D printers. Our raw materials reduce shrinkage and ensure objects match our customers’ precise specifications.
Tap into our expertise
Would you like to know more? Our Product Flashes give details on specific products or applications whilst our Lab Reports contain the latest findings in our laboratories – e.g. for 3D printing, LED and digital or inkjet printing. You can find out more at www.rahn-group.com/en/energycuring/news/.
Use our laboratories
Would you like to work together with us to find out what works and to produce the optimum result for your project? Our laboratories are at your disposal – for training your staff as well, should you wish.